-
EQFS: Integrated controller Slider type
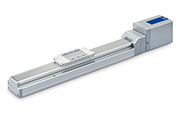 |
*Easy to set up, just like air equipment! Two position stop with no programming required Three position stop with no programming required Cycle time can be set in all operating modes. *Downsized with Integrated Controller, Wiring saving, Labor saving · Programless· Reduced adjustment time *Annual CO2 emissions reduced by up to 60% through motor control optimization 5.8 ← 14.1 [kg-CO₂e/year] ∗ The numerical values vary depending on the operating conditions. *With internal battery-less absolute encoder Restart from the last stop position is possible after recovery of the power supply. Reduced maintenance (No need to manage or replace batteries) |
-
EQY: Integrated controller Rod type
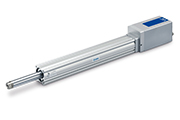 |
*Easy to set up, just like air equipment! Two position stop with no programming required Three position stop with no programming required Cycle time can be set in all operating modes. *Downsized with Integrated Controller, Wiring saving, Labor saving · Programless· Reduced adjustment time *Annual CO2 emissions reduced by up to 60% through motor control optimization 5.8 ← 14.1 [kg-CO₂e/year] ∗ The numerical values vary depending on the operating conditions. *With internal battery-less absolute encoder Restart from the last stop position is possible after recovery of the power supply. Reduced maintenance (No need to manage or replace batteries) |
-
EQYG: Integrated controller Guide Rod Type
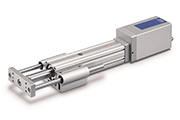 |
*Easy to set up, just like air equipment! Two position stop with no programming required Three position stop with no programming required Cycle time can be set in all operating modes. *Downsized with Integrated Controller, Wiring saving, Labor saving · Programless· Reduced adjustment time *With internal battery-less absolute encoder Restart from the last stop position is possible after recovery of the power supply. Reduced maintenance (No need to manage or replace batteries)
*Compact integration of guide rods Achieves lateral load resistance and high non-rotating accuracy *Compatible with sliding bearings and ball bushing bearings Compatible with moment load and stopper (sliding bearings) |
-
LE2FS: Compatible with Manifold Controller Slider type/Ball Screw Drive
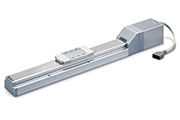 |
*Compatible with manifold controller Up to 16 axes can be connected. *Restart from the last stop position is possible. *Easy operation restart after recovery of the power supply The position information is held by the encoder even when the power supply is turned off. A return to origin operation is not necessary when the power supply is recovered. *No battery is installed. Reduced maintenance No battery is used to store the position information. There is no need to manage spare batteries or replacement maintenance. *Max. work load: 80 kg (Horizontal), 40 kg(Vertical) *Positioning repeatability: ±0.015 mm (H lead: ±0.02mm) |
-
LE2FB: Compatible with Manifold Controller Slider type/Belt Drive
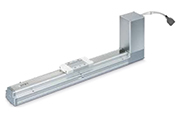 |
*Compatible with manifold controller Up to 16 axes can be connected. *Restart from the last stop position is possible. *Easy operation restart after recovery of the power supply The position information is held by the encoder even when the power supply is turned off. A return to origin operation is not necessary when the power supply is recovered. *No battery is installed. Reduced maintenance No battery is used to store the position information. There is no need to manage spare batteries or replacement maintenance. *Max. stroke: 2000 mm |
-
LE2Y: Compatible with Manifold Controller Rod type
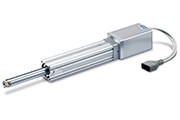 |
*Compatible with manifold controller Up to 16 axes can be connected. *Battery-less absolute encoder mounted. *Restart from the last stop position is possible. *Easy operation restart after recovery of the power supply The position information is held by the encoder even when the power supply is turned off. A return to origin operation is not necessary when the power supply is recovered. *No battery is installed. Reduced maintenance No battery is used to store the position information. There is no need to manage spare batteries or replacement maintenance. *Max. work load: 100 kg (Horizontal), 46 kg(Vertical) *Positioning repeatability: ±0.02 mm |
-
LE2YG: Compatible with Manifold Controller Guide Rod Type
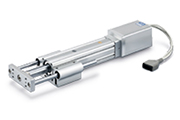 |
*Compatible with manifold controller Up to 16 axes can be connected. *Battery-less absolute encoder mounted. *Restart from the last stop position is possible. *Easy operation restart after recovery of the power supply The position information is held by the encoder even when the power supply is turned off. A return to origin operation is not necessary when the power supply is recovered. *No battery is installed. Reduced maintenance No battery is used to store the position information. There is no need to manage spare batteries or replacement maintenance. *Max. work load: 100 kg (Horizontal), 44 kg(Vertical) *Positioning repeatability: ±0.02 mm *Compact integration of guide rods Achieves lateral load resistance and high non-rotating accuracy *Compatible with sliding bearings and ball bushing bearings Compatible with moment load and stopper (sliding bearings) |
-
LE2R: Compatible with Manifold Controller Rotary table type

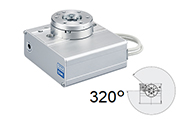 |
*Compatible with manifold controller Up to 16 axes can be connected. *Restart from the last stop position is possible. *Easy operation restart after recovery of the power supply The position information is held by the encoder even when the power supply is turned off. A return to origin operation is not necessary when the power supply is recovered. *No battery is installed. Reduced maintenance No battery is used to store the position information. There is no need to manage spare batteries or replacement maintenance.
*Rotation angle: 320º, 180º , 90º *Space saving: Built-in step motor *Shock-less/high speed actuation Max. speed: 600°/sec Max. acceleration/deceleration: 3000º/sec²
|
-
LEKFS: High Rigidity and High Precision Slider Type
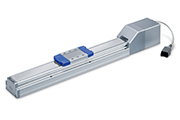 |
*Circular arc grooves allow for high rigidity and high precision. *Moment resistance: Improved by up to 61% *Table displacement: Reduced by up to 50%
Battery-less Absolute Encoder Type *With internal battery-less absolute encoder Restart from the last stop position is possible after recovery of the power supply. Reduced maintenance (No need for control or replacement) *Positioning repeatability: ±0.01 mm
High performance battery-less absolute (Step motor 24 VDC) *Cycle time can be reduced. Cycle time: Reduced by 39% compared with the existing model *Acceleration/Deceleration: 10000 mm/s2 (334% increase compared with the existing model) *Max. speed: 1500 mm/s (Improved by 25% compared with the existing model) *With internal battery-less absolute encoder Restart from the last stop position is possible after recovery of the power supply. Reduced maintenance (No need for control or replacement)
AC Servo Motor *High output motor (100/200/400 W) *Improved high speed transfer ability *High acceleration/deceleration (20000 mm/s2) *Pulse input type *With internal absolute encoder *Positioning repeatability: ±0.01 mm |
-
LEFS: Slider Type/Ball Screw Drive
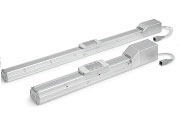 |
Step Motor (Servo/24 VDC) / Servo Motor (24 VDC) *Max. work load: 65 kg *Positioning repeatability: ±0.015 mm (High precision type)
AC Servo Motor *High output motor (100/200/400 W) *Improved high speed transfer ability *High acceleration/deceleration (20000 mm/s2) *Pulse input type *With internal absolute encoder *Positioning repeatability: ±0.01 mm (High precision type)
Battery-less Absolute Encoder Type *Restart from the last stop position is possible. *Easy operation restart after recovery of the power supply The position information is held by the encoder even when the power supply is turned off. A return to origin operation is not necessary when the power supply is recovered. *No battery is installed. Reduced maintenance No battery is used to store the position information. There is no need to manage spare batteries or replacement maintenance. *Max. work load: 65 kg *Positioning repeatability: ±0.015 mm (High precision type)
High performance Step motor (Servo/24 VDC) *Cycle time can be reduced. Cycle time: Reduced by 39% (0.57 s ← 0.93 s) compared with the existing model *Acceleration/Deceleration: 10000 mm/s2 (334% increase compared with the existing model) *Max. speed: 1500 mm/s (Improved by 25% compared with the existing model)
High performance battery-less absolute (Step motor 24 VDC) *Cycle time can be reduced. Cycle time: Reduced by 39% (0.57 s ← 0.93 s) compared with the existing model *Acceleration/Deceleration: 10000 mm/s2 (334% increase compared with the existing model) *Max. speed: 1500 mm/s (Improved by 25% compared with the existing model) *Easy operation restart after recovery of the power supply The position information is held by the encoder even when the power supply is turned off. A return to origin operation is not necessary when the power supply is recovered. *No battery is installed. Reduced maintenance No battery is used to store the position information. There is no need to manage spare batteries or replacement maintenance. |
-
LEFB: Slider Type/Belt Drive
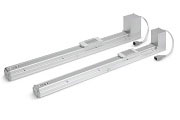 |
Step Motor (Servo/24 VDC), Servo Motor (24 VDC) *Max. stroke: 2000 mm *Max. speed: 2000 mm/s *Positioning repeatability: ±0.08 mm
AC Servo Motor *Max. speed: 2000 mm/s *Max. stroke: 3000 mm *Max. acceleration/deceleration: 20000 mm/s2 *Pulse input type *With internal absolute encoder *Positioning repeatability: ±0.06 mm
Battery-less Absolute Encoder Type *Restart from the last stop position is possible. *Easy operation restart after recovery of the power supply The position information is held by the encoder even when the power supply is turned off. A return to origin operation is not necessary when the power supply is recovered. *No battery is installed. Reduced maintenance No battery is used to store the position information. There is no need to manage spare batteries or replacement maintenance. *Max. stroke: 2000 mm *Max. speed: 2000 mm/s *Positioning repeatability: ±0.08 mm |
-
LET: Large Slider Type/Belt Drive
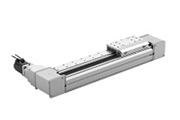 |
*Max. work load: 240 kg (Size 100), 75 kg (Size 80) *Stroke: Up to 3000 mm (Standard) *Max. speed: 4000mm/s (Size 100), 2160mm/s (Size 80) *Max. acceleration/deceleration: 20000 mm/s² *Simplified belt replacement *Solid state auto switches are mountable. |
-
LEJS: High Rigidity Slider Type/Ball Screw Drive
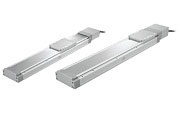 |
*Low profile/Low center of gravity: Height reduced by approx. 36% (Reduced by 32 mm) *Max. work load: Horizontal: 400 kg, Vertical: 80 kg *Positioning repeatability: ±0.02 mm *Max. speed: 2300 mm/s *Max. acceleration/deceleration: 20000 mm/s2 *Supports 750 W motor output |
-
LEJB: High Rigidity Slider Type/Belt Drive
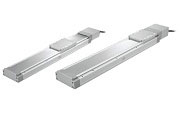 |
*Max. stroke: 3000 mm *Max. speed: 3000 mm/s *Max. acceleration/deceleration: 20000 mm/s2 |
-
LEL: Guide Rod Slider/Belt Drive
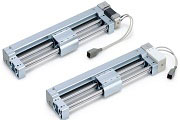 |
*Low profile/Flat: Height 48 mm *Profile reduced by the side mounting of the motor. No interference with the motor, even with large workpieces. *Auto switch mountable (Made to order) *Max. stroke: 1000 mm *Transfer speed: 1000 mm/s *Positioning repeatability: ±0.08 mm |
-
LEMB: Low Profile Slider Type/Basic
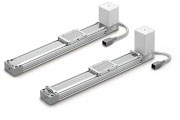 |
*Low-profile, Low center of gravity *Can be combined with various guides *High maintainability *Motor mounting position: Select from above or below, right or left *Solid state auto switches can be mounted for limit confirmation and intermediate signal confirmation. *Selectable controllability (Controller) Complete control like an air cylinder (Allows for a 12 point intermediate stop) Easy position setting by value input |
-
LEMC: Low Profile Slider Type/Cam follower guide
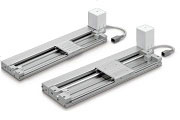 |
*Low-profile, Low center of gravity Table height: 28 mm (In the case of size 25) *Can be combined with various guides *High maintainability *Motor mounting position: Select from above or below, right or left *Solid state auto switches can be mounted for limit confirmation and intermediate signal confirmation. *Selectable controllability (Controller) Complete control like an air cylinder (Allows for a 12 point intermediate stop) Easy position setting by value input |
-
LEMH: Low Profile Slider Type/Linear guide (Single axis)
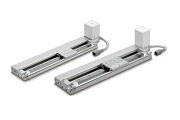 |
*Low-profile, Low center of gravity Table height: 28 mm (In the case of size 25) *Can be combined with various guides *High maintainability *Motor mounting position: Select from above or below, right or left *Solid state auto switches can be mounted for limit confirmation and intermediate signal confirmation. *Selectable controllability (Controller) Complete control like an air cylinder (Allows for a 12 point intermediate stop) Easy position setting by value input *Provides more moment resistance than the LEMC cam follower guide type. |
-
LEMHT: Low Profile Slider Type/Linear guide (Double axis)
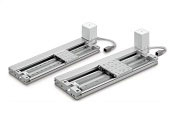 |
*Low-profile, Low center of gravity Table height: 28 mm (In the case of size 25) *Can be combined with various guides *High maintainability *Motor mounting position: Select from above or below, right or left *Solid state auto switches can be mounted for limit confirmation and intermediate signal confirmation. *Selectable controllability (Controller) Complete control like an air cylinder (Allows for a 12 point intermediate stop) Easy position setting by value input *Provides more moment resistance than the LEMH linear guide single axis type. |
-
LEFSW: Slider type/Dust-tight/Water-jet-proof(IP65 Equivalent)
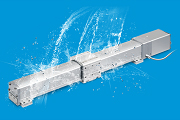 |
┟᪳dust-tight and water-jet-resistant (IP65 equivalent) slider type product Newly developed special wear-resistant seal band A special wear-resistant seal band is mounted on the bottom to prevent dust and water from entering the inside of the product. * With internal battery-less absolute encoder Restart from the last stop position is possible after recovery of the power supply. Reduced maintenance (No need to manage or replace batteries) * Work load: Max. 65 kg * Stroke: Max. 1200 mm (Size 40)
IP65 Equivalence The dust-tight and water-jet-resistant performance of this product's. Motor part is equivalent to IP65. However, since the actuator part has an opening, an IP65 rating for the actuator body cannot be guaranteed. |
-
LEY: Rod Type
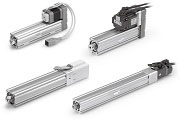 |
Step Motor (Servo/24 VDC), Servo Motor (24 VDC) *Long stroke: Max. 500 mm *Direct mounting: 3 directions, Bracket mounting: 3 types *Auto switch can be mounted. *Speed control/Positioning: Max. 64 points *Either positioning or pushing control can be selected. It is possible to hold the actuator with the rod pushing on a workpiece, etc. *Positioning repeatability: ±0.02 mm or less *Dust-tight/Water-jet-proof (IP65)
AC Servo Motor *High output motor (100/200/400 W) *Improved high speed transfer ability *High acceleration compatible (5000 mm/s2) *Pulse input type *With internal absolute encoder *Positioning repeatability: ±0.02 mm or less
Battery-less absolute (Step motor 24 VDC) *Restart from the last stop position is possible. *Easy operation restart after recovery of the power supply The position information is held by the encoder even when the power supply is turned off. A return to origin operation is not necessary when the power supply is recovered. *No battery is installed. Reduced maintenance No battery is used to store the position information. There is no need to manage spare batteries or replacement maintenance. *Long stroke: Max. 500 mm *Direct mounting: 3 directions, Bracket mounting: 3 types *Auto switch can be mounted. *Either positioning or pushing control can be selected. It is possible to hold the actuator with the rod pushing on a workpiece, etc. *Positioning repeatability: ±0.02 mm or less
High performance Step motor (Servo/24 VDC) *Cycle time can be reduced. Cycle time: Reduced by 44% compared with the existing model *Acceleration/Deceleration: 10000 mm/s2 (334% increase compared with the existing model) *Max. speed: 800 mm/s (Improved by 60% compared with the existing model)
High performance battery-less absolute (Step motor 24 VDC) *Cycle time can be reduced. Cycle time: Reduced by 33% compared with the existing model *Acceleration/Deceleration: 10000 mm/s2 (334% increase compared with the existing model) *Max. speed: 700 mm/s (Improved by 40% compared with the existing model) *Easy operation restart after recovery of the power supply The position information is held by the encoder even when the power supply is turned off. A return to origin operation is not necessary when the power supply is recovered. *No battery is installed. Reduced maintenance No battery is used to store the position information. There is no need to manage spare batteries or replacement maintenance. |
-
LEYG: Guide Rod Type
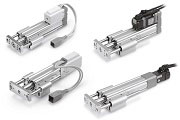 |
Step Motor (Servo/24 VDC), Servo Motor (24 VDC) *Compact integration of guide rods Achieves lateral load resistance and high non-rotating accuracy *Lateral end load: 5 times more (Compared with a rod type, size 25, 100 stroke) *Compatible with sliding bearings and ball bushing bearings Compatible with moment load and stopper (sliding bearings) *Speed control/Positioning: Max. 64 points *Either positioning or pushing control can be selected. It is possible to hold the actuator with the rod pushing on a workpiece, etc. *Positioning repeatability: ±0.02 mm or less
AC Servo Motor *High output motor (100/200 W) *Improved high speed transfer ability *High acceleration/deceleration compatible (5000 mm/s2) *Pulse input type *With internal absolute encoder
Battery-less absolute (Step motor 24 VDC) *Restart from the last stop position is possible. *Easy operation restart after recovery of the power supply The position information is held by the encoder even when the power supply is turned off. *No battery is installed. Reduced maintenance No battery is used to store the position information. There is no need to manage spare batteries or replacement maintenance. *Compact integration of guide rods Achieves lateral load resistance and high non-rotating accuracy *Lateral end load: 5 times more (Compared with a rod type, size 25, 100 stroke) *Compatible with sliding bearings and ball bushing bearings Compatible with moment load and stopper (sliding bearings) *Either positioning or pushing control can be selected. It is possible to hold the actuator with the rod pushing on a workpiece, etc. *Positioning repeatability: ±0.02 mm or less |
-
LEG: High Rigidity Guide Rod Type
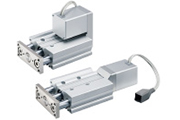 |
*Maximum material capacity to be conveyed: 75 kg (size 25), 100 kg (size 32), 150 kg (size 40) *Compatible with high tact controller Maximum acceleration/deceleration speed: 5000 mm/s2 *Battery-less absolute encoder mounted *Compatible with auto switch (straight only) For limit confirmation and intermediate signal confirmation *Guide unit integrated into a compact unit for improved lateral load capacity |
-
LES: Electric Slide Table Compact Type
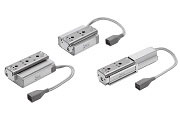 |
Step Motor (Servo/24 VDC), Servo Motor (24 VDC) *Compact: Workpiece mounting surface height reduced by up to 12% compared with the LESH *Vertical work load: Increased by up to 50% *Lightweight: Reduced by up to 29% *Max. pushing force: 180 N *Positioning repeatability: ±0.05 mm *Cycle time can be reduced. Max. acceleration/deceleration: 5000 mm/s2 Max. speed: 400 mm/s
Battery-less absolute (Step motor 24 VDC) *Restart from the last stop position is possible. *Easy operation restart after recovery of the power supply The position information is held by the encoder even when the power supply is turned off. A return to origin operation is not necessary when the power supply is recovered. *No battery is installed. Reduced maintenance No battery is used to store the position information. There is no need to manage spare batteries or replacement maintenance. *Max. pushing force: 180 N *Positioning repeatability: ±0.05 mm *Cycle time can be reduced. Max. acceleration/deceleration: 5000 mm/s2 Max. speed: 400 mm/s |
-
LESH: Electric Slide Table High Rigidity Type
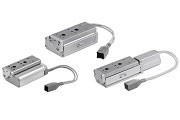 |
Step Motor (Servo/24 VDC), Servo Motor (24 VDC) *Compact: Workpiece mounting surface height reduced by up to 12% compared with the LESH *Vertical work load: Increased by up to 50% *Lightweight: Reduced by up to 29% *Max. pushing force: 180 N *Positioning repeatability: ±0.05 mm *Cycle time can be reduced. Max. acceleration/deceleration: 5000 mm/s2 Max. speed: 400 mm/s
Battery-less absolute (Step motor 24 VDC) *Restart from the last stop position is possible. *Easy operation restart after recovery of the power supply The position information is held by the encoder even when the power supply is turned off. A return to origin operation is not necessary when the power supply is recovered. *No battery is installed. Reduced maintenance No battery is used to store the position information. There is no need to manage spare batteries or replacement maintenance. *Integrated guide rail and table Uses a recirculating linear guide for high rigidity and high precision *Reduced cycle time Max. acceleration/deceleration: 5000 mm/s2 Max. speed: 400 mm/s *Max. pushing force: 180 N *Positioning repeatability: ±0.05 mm |
-
LESYH: Slide Table/High Precision Type
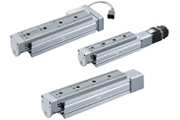 |
Battery-less Absolute Encoder Type *Restart from the last stop position is possible. *Easy operation restart after recovery of the power supply The position information is held by the encoder even when the power supply is turned off. A return to origin operation is not necessary when the power supply is recovered. *No battery is installed. Reduced maintenance No battery is used to store the position information. There is no need to manage spare batteries or replacement maintenance. *Improved positioning repeatability due to the adoption of a ball screw drive. Positioning repeatability: ±0.01 mm *Lost motion: 0.1 mm or less *Increased vertical work load: 5 times or more
High performance battery-less absolute (Step motor 24 VDC) *Cycle time can be reduced. Cycle time: Reduced by 39% compared with the existing model *Acceleration/Deceleration: 10000 mm/s2 (200% increase compared with the existing model) *Max. speed: 800 mm/s (Improved by 200% compared with the existing model) *Easy operation restart after recovery of the power supply The position information is held by the encoder even when the power supply is turned off. A return to origin operation is not necessary when the power supply is recovered. *No battery is installed. Reduced maintenance No battery is used to store the position information. There is no need to manage spare batteries or replacement maintenance.
AC Servo Motor *High output motor (100/200) *Improved high speed transfer ability *High acceleration/deceleration (20000 mm/s2) *Positioning repeatability: ±0.01 mm |
-
LEPY: Miniature Rod Type
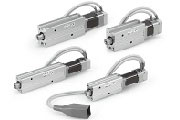 |
*Compact and lightweight W 20.5 mm x H 30 mm x L 125.6 mm, Weight 240 g(LEPY6[]-25) *Max. pushing force: 50 N *Positioning repeatability: ±0.05 mm *It is possible to set the position, speed, and force. (64 points) *Max. speed (Horizontal): 350 mm/s |
-
LEPS: Miniature Slide Table Type
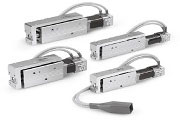 |
*Compact and lightweight W 21 mm x H 41 mm x L 138.6 mm, Weight 290 g (LEPS6[]-25) *Max. pushing force: 50 N *Positioning repeatability: ±0.05 mm *It is possible to set the position, speed, and force. (64 points) *Max. speed (Horizontal): 350 mm/s |
-
LER: Rotary Table Basic Type
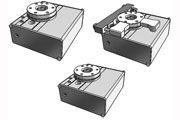 |
Step Motor (Servo/24 VDC), Servo Motor (24 VDC) *Rotation angle: 320º, 310º, 180º , 90º *Low profile: Height 42 mm (LER10) *Space saving: Built-in step motor *Shock-less/high speed actuation Max. speed: 420°/sec (7.33 rad/sec) Max. acceleration/deceleration: 3000º/sec2 (52.36 rad/sec2) *It is possible to set the speed, acceleration/deceleration, and position. Max. 64 points *Energy saving: Automatic 40% power reduction after the table has stopped *Easy setting: Data can be set with only 2 items, position and speed. The controller is already set with the data of the actuator. (The actuator and controller are provided as a set.)
Battery-less absolute (Step motor 24 VDC) *Restart from the last stop position is possible. *Easy operation restart after recovery of the power supply The position information is held by the encoder even when the power supply is turned off. A return to origin operation is not necessary when the power supply is recovered. *No battery is installed. Reduced maintenance No battery is used to store the position information. There is no need to manage spare batteries or replacement maintenance. *Rotation angle: 320º, 180º, 90º *Space saving: Built-in step motor *Shock-less/high speed actuation Max. speed: 420º/sec Max. acceleration/deceleration: 3000º/sec2 |
-
LERH: Rotary Table High-Precision Type
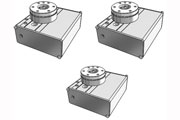 |
*Rotation angle: 320º, 310º, 180º , 90º *The movement in the table’s radial thrust direction is reduced. *Positioning repeatability: ±0.03° *Low profile: Height 42 mm (LER10) *Space saving: Built-in step motor *Shock-less/high speed actuation Max. speed: 420°/sec (7.33 rad/sec) Max. acceleration/deceleration: 3000º/sec2 (52.36 rad/sec2) *It is possible to set the speed, acceleration/deceleration, and position. Max. 64 points *Energy saving: Automatic 40% power reduction after the table has stopped *Easy setting: Data can be set with only 2 items, position and speed. The controller is already set with the data of the actuator. (The actuator and controller are provided as a set.)
Battery-less absolute (Step motor 24 VDC) *Restart from the last stop position is possible. *Easy operation restart after recovery of the power supply The position information is held by the encoder even when the power supply is turned off. A return to origin operation is not necessary when the power supply is recovered. *No battery is installed. Reduced maintenance No battery is used to store the position information. There is no need to manage spare batteries or replacement maintenance. *Rotation angle: 320º, 180º, 90º *Space saving: Built-in step motor *Shock-less/high speed actuation Max. speed: 420º/sec Max. acceleration/deceleration: 3000º/sec2 |
-
LER-1: Rotary Table Basic type/Continuous Rotation Specification
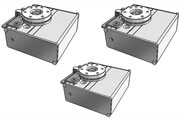 |
*Rotation angle: 360º *Angle setting range:±20000000° *Low profile: Height 42 mm (LER10) *Space saving: Built-in step motor *Shock-less/high speed actuation Max. speed: 420°/sec (7.33 rad/sec) Max. acceleration/deceleration: 3000º/sec2 (52.36 rad/sec2) *It is possible to set the speed, acceleration/deceleration, and position. Max. 64 points *Energy saving: Automatic 40% power reduction after the table has stopped *Easy setting: Data can be set with only 2 items, position and speed. The controller is already set with the data of the actuator. (The actuator and controller are provided as a set.) |
-
LERH-1: Rotary Table High-Precision Type/Continuous Rotation Specification
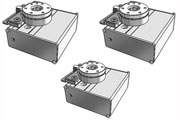 |
Step Motor (Servo/24 VDC), Servo Motor (24 VDC) *Rotation angle: 360º *Angle setting range:±20000000° *The movement in the table’s radial thrust direction is reduced. *Positioning repeatability: ±0.03° *Low profile: Height 42 mm (LER10) *Space saving: Built-in step motor *Shock-less/high speed actuation Max. speed: 420°/sec (7.33 rad/sec) Max. acceleration/deceleration: 3000º/sec2 (52.36 rad/sec2) *It is possible to set the speed, acceleration/deceleration, and position. Max. 64 points *Energy saving: Automatic 40% power reduction after the table has stopped *Easy setting: Data can be set with only 2 items, position and speed. The controller is already set with the data of the actuator. (The actuator and controller are provided as a set.) |
-
LEHZ: Gripper 2-Finger Type
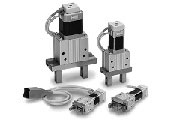 |
*Easy setting: Data can be set with only 2 items, position and force. The controller is already set with the data of the actuator. (The actuator and controller are provided as a set.) *Equipped with a drop prevention function *The self-lock mechanism reduces power consumption. *Equipped with a gripping check function *It is possible to set the position, speed, and force. (64 points) |
-
LEHZJ: Gripper 2-Finger Type/With Dust Cover
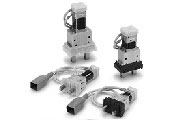 |
*Easy setting: Data can be set with only 2 items, position and force. The controller is already set with the data of the actuator. (The actuator and controller are provided as a set.) *Equipped with a drop prevention function (All series come equipped with a self-lock mechanism.) *The self-lock mechanism reduces power consumption. *Equipped with a gripping check function *It is possible to set the position, speed, and force. (64 points) |
-
LEHF: Gripper 2-Finger Type/Long Stroke
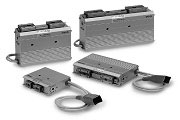 |
Step Motor (Servo/24 VDC) *Easy setting: Data can be set with only 2 items, position and force. The controller is already set with the data of the actuator. (The actuator and controller are provided as a set.) *Equipped with a drop prevention function *The self-lock mechanism reduces power consumption. *Equipped with a gripping check function *It is possible to set the position, speed, and force. (64 points)
Battery-less absolute (Step motor 24 VDC) *Restart from the last stop position is possible. *Easy operation restart after recovery of the power supply The position information is held by the encoder even when the power supply is turned off. A return to origin operation is not necessary when the power supply is recovered. *No battery is installed. Reduced maintenance No battery is used to store the position information. There is no need to manage spare batteries or replacement maintenance. *Equipped with a drop prevention function (All series come equipped with a self-lock mechanism.) *The self-lock mechanism reduces power consumption. *Equipped with a gripping check function |
-
LEHS: Gripper 3-Finger type
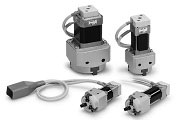 |
*Easy setting: Data can be set with only 2 items, position and force. The controller is already set with the data of the actuator. (The actuator and controller are provided as a set.) *Equipped with a drop prevention function (All series come equipped with a self-lock mechanism.) *The self-lock mechanism reduces power consumption. *Equipped with a gripping check function *It is possible to set the position, speed, and force. (64 points) |
-
HF2A-LEY: Rod Type/Dust-tight/Water-jet-proof(IP69K Equivalent)
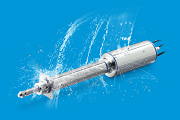 |
*Enclosure: Dust-tight/Water-jet-proof(IP69K Equivalent) *Grease: NSF H1 grease *Products Utilizing US FDA/Japan Food Sanitation Act compliant material *Design for better liquid flow and less residual liquid accumulation
IP69K is the degree of protection against dust and high pressure hot water washdown specified in DIN 40050-9 and currently specified in ISO 20653 and JIS D 5020. |
-
25A-LEKFS: Compatible with secondary batteries/Slider Type/Ball Screw Drive
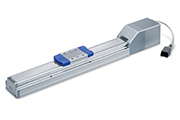 |
The product that is compatible with the environment of the secondary battery manufacturing process. For the 25A- series, there is a restriction on the use of copper and zinc as main components in the metal materials used. *Copper and zinc materials are used for the motors, cables, controllers/drivers. Applicable for use at −70°C. *Uses grease compatible with low dew points.
*Circular arc grooves allow for high rigidity and high precision. *Moment resistance: Improved by up to 61% *Table displacement: Reduced by up to 50% |
-
25A-LEFS: Compatible with secondary batteries/High Rigidity Slider Type/Ball Screw Drive
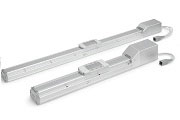 |
The product that is compatible with the environment of the secondary battery manufacturing process. For the 25A- series, there is a restriction on the use of copper and zinc as main components in the metal materials used. *Copper and zinc materials are used for the motors, cables, controllers/drivers. Applicable for use at −70°C. *Uses grease compatible with low dew points. |
-
25A-LEJS: Compatible with secondary batteries/High Rigidity and High Precision Slider Type
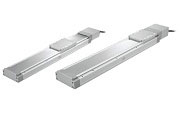 |
The product that is compatible with the environment of the secondary battery manufacturing process. For the 25A- series, there is a restriction on the use of copper and zinc as main components in the metal materials used. *Copper and zinc materials are used for the motors, cables, controllers/drivers. Applicable for use at −70°C. *Uses grease compatible with low dew points.
*Low profile/Low center of gravity: Height reduced by approx. 36% (Reduced by 32 mm) |
-
25A-LEY: Compatible with secondary batteries/Rod Type
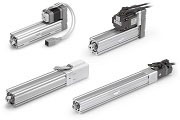 |
The product that is compatible with the environment of the secondary battery manufacturing process. For the 25A- series, there is a restriction on the use of copper and zinc as main components in the metal materials used. *Copper and zinc materials are used for the motors, cables, controllers/drivers. Applicable for use at −70°C. *Uses grease compatible with low dew points. |
-
25A-LEYG: Compatible with secondary batteries/Guide Rod Type
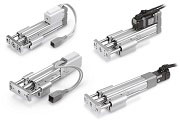 |
The product that is compatible with the environment of the secondary battery manufacturing process. For the 25A- series, there is a restriction on the use of copper and zinc as main components in the metal materials used. *Copper and zinc materials are used for the motors, cables, controllers/drivers. Applicable for use at −70°C. *Uses grease compatible with low dew points.
*Compact integration of guide rods Achieves lateral load resistance and high non-rotating accuracy *Lateral end load: 5 times more (Compared with a rod type, size 25, 100 stroke) *Compatible with sliding bearings and ball bushing bearings Compatible with moment load and stopper (sliding bearings) |
-
11-LEFS: Clean Series/Slider Type/Ball Screw Drive
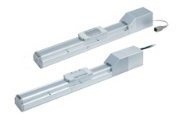 |
VISO Class 4* (ISO 14644-1) * Built-in vacuum piping * It is possible to mount the main body without removing the external cover, etc. * Body-integrated linear guide specification * Changes depending on the suction flow rate
Step Motor (Servo/24 VDC), Servo Motor (24 VDC) ・Max. work load: 60 kg ・Positioning repeatability: ±0.02 mm
AC Servo Motor ・High output motor (100/200/400 W) ・Improved high speed transfer ability ・High acceleration/deceleration (20000 mm/s²) ・Pulse input type ・With internal absolute encoder ・Positioning repeatability: ±0.02 mm |
-
11-LEJS: Clean Series/High Rigidity Slider Type/Ball Screw Drive
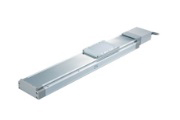 |
VISO Class 4* (ISO 14644-1) ・Built-in vacuum piping ・It is possible to mount the main body without removing the external cover, etc. ・Body-integrated linear guide specification * Changes depending on the suction flow rate
・Low profile/Low center of gravity: Height reduced by approx. 36% (Reduced by 32 mm) ・Max. work load: 85 kg ・Positioning repeatability: ±0.02 mm ・Max. acceleration/deceleration: 20000 mm/s² |